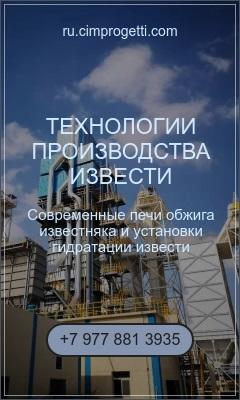
Подробно на www.cimprogetti.info
Известь (из греч. ἄσβεστος «неугасимый») — материал, получаемый путём обжига (не до расплава) карбонатных горных пород (известняков, мела). По химическому составу она почти полностью состоит из свободных оксидов кальция и магния с преимущественным содержанием СаО. Применяется в строительстве, а также для получения различных химических веществ, некоторые из которых также носят название «известь».
В зависимости от типа породы, из которой произведена известь, она может быть кальциевой, магнезиальной или доломитовой.
ИЗВЕСТНЯК, осадочная порода, сложенная преимущественно карбонатом кальция – кальцитом. Благодаря широкому распространению, легкости обработки и химическим свойствам известняк добывается и используется в большей степени, чем другие породы, уступая только песчано-гравийным отложениям. Известняки бывают разных цветов, включая черный, но чаще всего встречаются породы белого, серого цвета или имеющие коричневатый оттенок. Объемная плотность 2,2–2,7. Это мягкая порода, легко царапающаяся лезвием ножа. Известняки бурно вскипают при взаимодействии с разбавленной кислотой. В соответствии со своим осадочным происхождением имеют слоистое строение. Чистый известняк состоит только из кальцита (редко с небольшим содержанием другой формы карбоната кальция – арагонита). Присутствуют и примеси. Двойной карбонат кальция и магния – доломит – обычно содержится в переменных количествах, и возможны все переходы между известняком, доломитовым известняком и горной породой доломитом. В процессе отложения известняка водой привносятся также глинистые частицы, порода становится глинистой, стираются четкие границы между известняком, глинистым известняком и глинистым сланцем. Кремень тоже является обычной примесью; он нередко присутствует в форме желваков (кремневых конкреций) или в виде более или менее явно выраженных слоев. При метаморфизме, по мере того, как перекристаллизация кальцита охватывает всю породу и возникает мозаичная структура (агрегат из четко ограниченных плотно прилегающих друг к другу изометричных зерен приблизительно одинакового размера), известняк постепенно превращается в мрамор.
Существует много разновидностей известняка. Ракушечником называют скопления обломков раковин, сцементированных в ячеистый агрегат. Если раковины имеют микроскопическую величину, образуется слабосвязанная, мягкая, тонко крошащаяся, мажущая порода – мел. Оолитовый известняк состоит из мелких, размером с рыбьи икринки, сцементированных между собой шариков. Ядро каждого такого шарика-оолита может быть представлено песчинкой, обломком раковины или частицей какого-либо другого инородного материала. Если шарики более крупные, величиной с горошину, их называют пизолитами, а породу – пизолитовым известняком. Травертин – известняк, образовавшийся на поверхности в результате осаждения карбоната кальция (кальцита или арагонита) из воды углекислых источников. Если такие отложения сильно пористые (губчатые), их называют известковым туфом. Мергель представляет собой несцементированную смесь карбоната кальция и глины. Названия некоторых разновидностей известняка обусловлены возможным направлением его практического использования. Например, литографический известняк – это исключительно плотный, компактный и однородный камень, применяемый в литографии.
Хотя известняки могут образовываться в любых пресноводных и морских бассейнах, преобладающее большинство этих пород имеет морское происхождение. Иногда они осаждаются, подобно соли и гипсу, из воды испаряющихся озер и морских лагун, но, по-видимому, бóльшая часть известняков отложилась в морях, не испытавших интенсивного высыхания. По всей вероятности, формирование большинства известняков начиналось с извлечения живыми организмами карбоната кальция из морской воды (для построения раковин и скелетов). Эти остатки отмерших организмов в изобилии накапливаются на морском дне. Самым ярким примером аккумуляции карбоната кальция служат коралловые рифы. В некоторых случаях в известняке различимы и узнаваемы отдельные раковины. В результате волно-прибойной деятельности и под влиянием морских течений рифы разрушаются. К известковым обломкам на морском дне добавляется карбонат кальция, осаждающийся из насыщенной им воды. В образовании более молодых известняков участвует также кальцит, поступающий из разрушенных более древних известняков.
Известняки встречаются почти на всех материках, за исключением Австралии. Они сформировались в разные геологические эпохи. Мощность пластов варьирует от нескольких сантиметров до сотен метров. Известняки распространены в США и занимают 75% площади страны. В России известняки обычны в центральных районах европейской части, а также распространены на Кавказе, Урале и в Сибири.
Известняки (в широком понимании) имеют чрезвычайно многообразные области применения. Они используются в виде кускового известняка, щебня, штучного (пильного, стенового) и бутового камня, облицовочных плит, минеральной крошки, дробленого песка, минерального порошка, минеральной ваты, известняковой муки. Основные потребители – цементная промышленность (известняк, мел и мергель), строительство (получение строительной извести, бетонов, штукатурки, строительных растворов; кладка стен и фундаментов; декоративно-облицовочные работы и т.д.), дорожное и железнодорожное строительство, каменная наброска для защиты берегов и гидротехнических сооружений, металлургия (известняк и доломит – флюсы и огнеупоры, переработка нефелиновых руд на глинозем, цемент и соду), сельское хозяйство (известняковая мука в агротехнике и животноводстве), нефте- и коксохимическая, пищевая (особенно сахарная), целлюлозно-бумажная, стекольная (известняк, мел, доломит), кожевенная (известняк), резиновая, кабельная, лакокрасочная промышленность (мел как наполнитель). Другие области применения – полировка изделий из цветных металлов и перламутра (известняк), электросварка (мел для покрытия электродов), писчие мелки (мел), теплоизоляция строительных конструкций и технологического оборудования (минеральная вата) и т.д.
В России известняк добывается карьерами в Подмосковье, Ленинградской (облицовочный), Архангельской, Вологодской, Тульской, Белгородской, Воронежской областях, в Предуралье (Пермская область) и Поволжье, Краснодарском крае, на Северном Кавказе, на Урале, в ряде районов Восточной Сибири. Из подмосковных мячковских известняков возводились храмы и другие постройки Москвы белокаменной. Сырьевые ресурсы карбонатного сырья (известняка, мела, мергеля, доломита) в стране практически неисчерпаемы, хотя распределены очень неравномерно. В Донецкой области на Украине находится крупнейшее в Европе Еленовское месторождение известняка и доломита.
Ввод известняка и доломитизированного известняка в агломерационную шихту позволяет получать офлюсованный агломерат. Вывод известняка из доменной шихты приводит к экономии значительного количества тепла, затрачиваемого ранее на диссоциацию карбонатов, и к соответствующей экономии кокса. Экономический эффект от применения офлюсованного агломерата достигается за счёт того, что при агломерации на реакции диссоциации затрачивается тепло, выделяемое в спекаемом слое при горении гораздо более дешевого, чем кокс, топлива (коксовая мелочь, антрацитовый штыб, тощий уголь). Применение офлюсованного агломерата позволяет улучшить шлакообразование, а также уменьшить содержание диоксида углерода в печных газах, то есть повысить их восстановительную способность и улучшить шлакообразование[
Известь – материал, применяемый в большинстве существующих отраслей, будь то промышленность или пищевая сфера. Незаменим известняк и в металлургии. В этой отрасли он используется как очищающий компонент, удаляющий лишнюю влагу и ненужные вещества из сплава, чтобы качество стали было еще более высоким.
Производство металлов
В металлургической промышленности, как правило, применяется известь негашеная, чтобы очистить металл от фосфорных, серных или кремниевых примесей, образующихся при введении кислорода в расплавленный чугун или сталь. Введение в процесс производства происходит в три этапа: во-первых для производства окатышей (полуфабрикаты железа, которые и загружаются в плавильную печь), во-вторых, очищают материал от серы перед плавкой, и в-третьих: после того, как к плавленому материалу примешивается кислород, известь в твердом или измельченном состоянии добавляют в печи, чтобы образовались жесткие шлаки, которые легко можно удалить на данном этапе. Подобное использование делает сталь сверхчистой: именно в таком виде она больше всего ценится на рынке.
Известь, вяжущий материал, получаемый обжигом и последующей переработкой известняка, мела и других известково-магнезиальных горных пород. Чистая известь - бесцветный продукт; плохо растворимый в воде (около 0,1% при 20 °С); плотность около 3,4 г/см3.
Первоначально известь использовалась только для приготовления связывающих растворов при строительстве зданий. Со временем область применения ее расширялась, и теперь известь и вещества на ее основе используются во многих отраслях промышленности, сельском хозяйстве и даже в охране окружающей среды [4].
В металлургической промышленности известь позволяет очистить металл от фосфорных, серных или кремниевых примесей, образующихся при введении кислорода в расплавленный чугун или сталь. Введение в процесс производства происходит в три этапа: во-первых для производства окатышей (полуфабрикаты железа, которые и загружаются в плавильную печь), во-вторых, очищают материал от серы перед плавкой, и в-третьих: после того, как к плавленому материалу примешивается кислород, известь в твердом или измельченном состоянии добавляют в печи, чтобы образовались жесткие шлаки, которые легко можно удалить на данном этапе. Подобное использование делает сталь сверхчистой: именно в таком виде она больше всего ценится на рынке.
Активно применяют известь и для производства металлической продукции: в создании проволоки или формовых элементов она незаменима в качестве своего рода «смазки». В первом случае проволока без проблем протягивается сквозь матрицу, а готовое изделие без труда отходит от посыпанной «мелом» формы.
Освоено и использование негашеной извести в производстве цветмета: выплавка драгметаллов без нее не обходится. Известно, что золотую и серебряную руду на определенном этапе измельчают, смешивают с раствором цианида и известью. Последняя обеспечивает необходимый кислотный баланс, который препятствует испарению вредных веществ в атмосферу.
Не менее известные нам медь или свинец также производятся не без участия этого универсального материала. Вред от опасных испарений сокращается, когда они пропускаются через так называемое «известковое молоко» (водный раствор) [2].
По химическому составу известь должны удовлетворять требованиям, указанным в табл.1.
Таблица 1.
Технические требования к извести
Марка
Сорт
CaOобщ, %, не менее
Массовое содержание примеси, %, не более
SiO2
S
P
п.п.п.
ИФ-0
1
95
1,8
0,03
0,02
3
ИФ-1
1
93
1,8
0,05
0,02
5
2
90
2,0
0,05
0,02
7
ИФ-2
1
90
2,0
0,08
0,03
7
2
85
2,5
0,08
0,03
11
п.п.п. – потери массы при прокаливании продукта, эквивалент остаточному содержанию углекислого газа.
Сырьем для получения извести являются распространенные осадочные горные породы: известняки, доломиты, мел, доломитизированные известняки, содержащие не более 8 % глины. В сырье преобладает карбонат кальция СаС03, в небольшом количестве содержатся карбонат магния MgCCb и некоторые примеси. Сырье обжигают в шахтных или вращающихся печах при температуре 900... 1200 °С [1].
Наиболее широко применяют плотные известняки и мел. Плотные известняки часто имеют мелкокристаллическую структуру. Иногда приходится использовать высокопрочные кремнистые известняки. Мел представляет собой мягкую, легко растирающуюся известковую породу. Рыхлая структура мела облегчает его добычу, но затрудняет обжиг в шахтных печах, так как куски мела легко крошатся, а образующаяся мелочь, заполняя пространство между обжигаемыми кусками, ухудшает тягу. При обжиге мела во вращающихся печах затруднений не встречается [3].
Очень важный показатель качества извести - режим ее обжига. В табл.2 приведены физические свойства извести разных типов.
Таблица 2.
Физические свойства извести
Характер обжига
Реакционная способность, мин-с.
Объемная масса, г/см3
Объем пор, cм3/г
Поверхность пор, м2/г
мягкий
0-32
1,25
0,313
8,54
средний
1-45
1,66
0,279
5,12
жесткий
32-00
2,06
0,158
0,61
Данные таблицы свидетельствуют о том, что для ускорения процесса шлакообразования целесообразно использовать мягкообожженную известь с высокой реакционной способностью. Эта известь, получаемая во вращающихся печах или в печах кипящего слоя, имеет большое количество пор. Наличие последних облегчает диффузию легкоплавких компонентов шлака в глубинные слои куска извести и тем самым ускоряет ассимиляцию ее шлаком.
В последние годы наметилась тенденция к использованию в качестве шлакообразующего материала мягкообожженной доломитизированной извести, причем используют ее либо в смеси с обычной известью, либо отдельно.
При этом преследуются две цели: улучшение процесса шлакообразования и повышение стойкости футеровки конвертеров.
В связи с этим в конвертерном производстве за рубежом освоена специальная известь «Долотект» с содержанием около 6 % MgO, представляющая собой эвтектику CaO-MgO, температура плавления которой на 280°С ниже, чем CaO.
Многолетний опыт использования доломитизированной извести, получаемой из известняка Докучаевского флюсодоломитного комбината в конвертерном цехе Енакиевского металлургического завода, показал преимущества данной технологии [6].
Для получения такой извести, содержащей 5-8 % MgO, в одной вращающейся печи обжигают доломитизированный известняк, две другие печи перерабатывают обычный известняк. Известь из печей смешивается в потоке при выгрузке.
По технологии получения извести из известняка, он при движении по барабану проходит последовательно зоны сушки, подогрева до температуры 1123—1153 К (850— 880 °С), обжига и предварительного охлаждения. При обжиге плотных известняков зона сушки в печи отсутствует из-за малой влажности материала. Зона подогрева составляет обычно 50—70% длины печи, зона обжига равна 25—30%. Длина может регулироваться изменением длины факела горящего топлива. Далее из зоны обжига известь поступает в зону предварительного охлаждения, занимающую как правило около 5% длины печи. Окончательно охлаждение происходит в специальном холодильнике. Воздух, нагретый в холодильнике до 573—673 К (300—400 °С) остывшей известью, поступает в печь для горения топлива в качестве вторичного воздуха. Первичный воздух в количестве 15—20% от общего его расхода на горение подают через горелку. Для ускорения теплообмена в зоне подогрева устанавливают цепные и металлические ячейковые теплообменники. Можно также применять запечные теплообменники циклонного типа и в виде конвейерной решетки [7].
Достоинства вращающихся печей:
1) известь высокого качества;
2) использование любого сырья;
3) применение любого вида топлива;
4) получение любого вида извести (строительной, металлургической)
Недостатки:
1) большая металлоемкость;
2) большие капиталовложения;
3) значительный расход топлива (по сравнению с шахтными);
4) высокий расход электроэнергии (по сравнению с шахтными).
На основе анализа научно-исследовательской литературы, было выяснено, что к сырью для производства извести должны предъявляться следующие требования:
Чем выше содержание в известняке карбоната кальция, тем более высококачественная известь может быть выработана из него.
Качество карбонатных пород для производства извести в России регламентируется ОСТ 21-27-76 «Породы карбонатные для производства строительной извести». Основные требования этого документа приведены в таблице 3.
Таблица 3.
Требования к химическому составу карбонатного сырья для производства известковых вяжущих.
Содержание, %
Класс
А
Б
В
Г
Д
Е
Ж
СаСО3, не менее
92
86
77
72
52
47
72
MgСО3, не более
5
6
20
20
45
45
8
Глинистые примеси (SiO2+Al2O3+Fe2O3), не более
3
8
3
8
3
8
20
Физические свойства сырья (прочность, истирание) предопределяют выбор агрегата для обжига, а химический состав и количество примесей –выбор температуры обжига.
По механической прочности сырье характеризуется пределом прочности при сжатии, МПа: твердые породы — более 60, породы средней твердости — 30—60, мягкие породы — 10—30 и очень мягкие — менее 10. Для производства извести могут применяться твердые карбонатные породы в фракционированном виде со следующими размерами кусков (фракций), мм: 5—20; 20—40; 40—80; 80—120; 120— 180, а также мягкие без деления на фракции [5].